Tailored
Metal Testing > Hardness Testers > Tailored
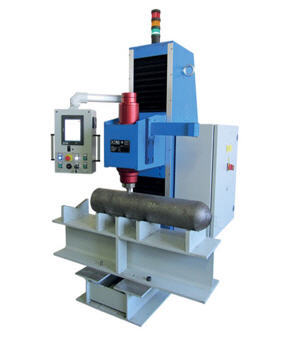
MRS BOT
Automatic hardness tester for production lines. Hardness measurements on gas bottles or tubes
Rockwell - Superficial Rockwell - Brinell - Vickers / Test loads from 3 to 3000 kgf (29,45 to 29421 N)
Automatic motorized vertical stroke programmable through PLC and automatic clamping system to block the sample from any distances.
In compliance with ASTM E10 and ISO 6506 standards.
Force loads controlled in closed loop by load cells and dwell time programmable slow or fast.
It is possible to include surface milling preparation tool 0,01 mm depth accuracy and roughness programmable by PLC.
LCD touch screen and large hard disk for data storage.
Remote controll via internet for service, additional operator training, quick diagnosis and software updates.
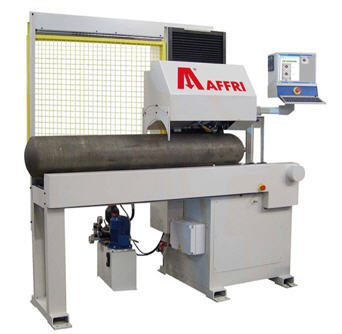
GAS BOTTLE
Automatic hardness tester for production lines. Hardness measurements on gas bottles or tubes
Rockwell - Brinell / Test loads from 10 to 3000 kgf (98,07 to 29421 N)
Complete hardness tester including surface preparation for conveyor lines and automatic hardness test cycles.
It is possible to program the surface preparation by cold milling procedure and the distance between multiple indentations for fully automatic repeated tests.
Brinell indentions autoreading with automatic optic system and autofocus.
Fully customizable in size and geometry, based on customer needs.
LCD touch screen console with large hard disk for data and test session storage.
MATRIX
Automatic hardness tests on crankshafts and camshafts in compliance with ISO 6508 e ASTM E18/E10/E103 standards
Rockwell - Superficial Rockwell - Brinell / Test loads from 1 to 250 kgf (9,807 to 2452 N)
The tester is made with a modular structure so that it can easily fit different size test pieces.
Equipped with movements on 3 independent axis and piece rotation of 360° to allow for an easy location of testing points.
Accurate and effective measurement even on the first test.
The indenter is very thin and long. A long and strong guide protects the indenter from shocks and allows tests very close to the connections.
With this hardness tester, it is possible to perform measurements directly during manufacturing process, so that the annealing oven staff can be informed in real time about test results.
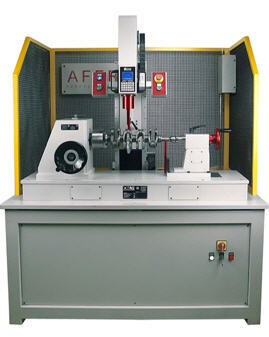
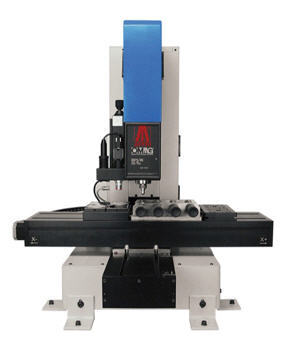
JOMINY
Automatic hardness tester for Jominy method in compliance with ASTM E18 and ISO 6508 standards
Jominy - Rockwell - Superficial Rockwell - Brinell / Test loads from 3 to 187,5 kgf (29,45 to 1839 N)
Designed for multiple specimen testing and double sized surface testing.
Single or multiple sample test pieces, can be tested automatically, conforming to ASTM E-18 specification.
Optical imaging system. Panoramic camera with a 5X objective, for a clear sample pattern starting origin, independent for each sample.
Automatic self calibration cycle, conforming to ASTM E-18- ISO 6508 on three test blocks (Hard, Medium & Soft) ranges.
Standardized test patterns are stored, in the on board database, for ease of instrument operation.
A customized test cycle can be created at anytime.
Optimize your test block surface area, giving you the ability to use the complete test block surface as well as time saving instrument validation
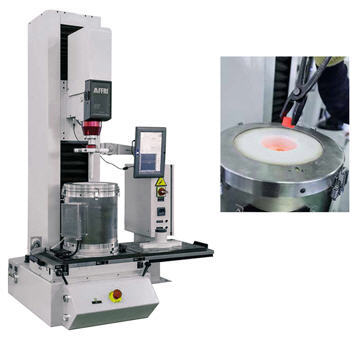
DAKO 300 HIGH TEMPERATURE
Hardness testing at high temperatures in accordance with ASTM E 18 and ISO 6508
Rockwell - Superficial Rockwell - Brinell / Test loads from 3 to 187,5 kgf (29,45 to 1839 N)
The temperature is programmable up to 980 ° C with steps of 1 ° C.
Multiple measurements remotely programmed, with single or multi test specimens.
Intercooler for faster cool down.
X/Y sliding table 100 X 300 mm.
300mm of indenter stroke with programmable speed and limit. Only one start command to approach and contact with the test and return
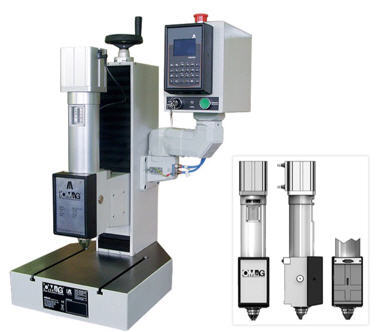
PRS
High speed automatic hardness tester for independent use of the measuring head in production department and lines.
Rockwell - Superficial Rockwell - Brinell/ Test loads from 3 to 187,5 kgf (29,45 to 1839 N)
Complete automatic hardness test cycle including the clamping of the piece, application of the load, hardness measurement, release of the piece, return to starting point and is ready for a new test.
High volume measurements, the tester can easily be introduced into the conveyor lines, yelding up to 1500 test per hour.
Direct readout in Rockwell or Brinell scales with electronic data output and automatic sorting of the results by low, ok or high hardness levels depending upon the preset tollerances.
The AFFRI company can plan and set up customized conveyor lines with the integrated hardness tester that will satisfy customer needs.
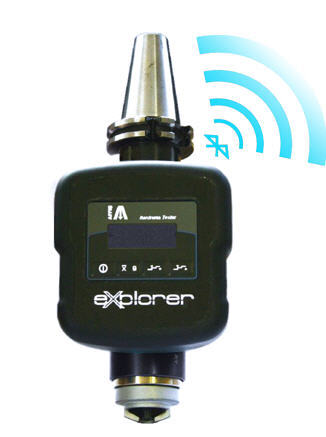
EXPLORER
Automatic hardness tester integrable inside of a CNC machine
Rockwell, Superficial Rockwell and Brinell / Test loads from 1 to 5,6 kgf (9,807 to 54,92 N)
Designed for being assembled as a common machine tool thanks to standard coupling cones ISO and DIN 30-40-50 or others on request.
Ideal to be inserted after a milling or grinding tool for reliable and precise hardness tests on prepared surfaces.
All measurement datas are transferred from the tester via Bluetooth, this allows you to place the support PC further away from the instrument for better ergonomics of the work place.
The software offers quick setting of all testing parameters and a complete set for analysing the data received from the instrument.
Graphic analysis, quick choice of testing scales, quick conversions and the ability to save real time statistic sessions, which allows for quick and functional analysis of the tests carried out.
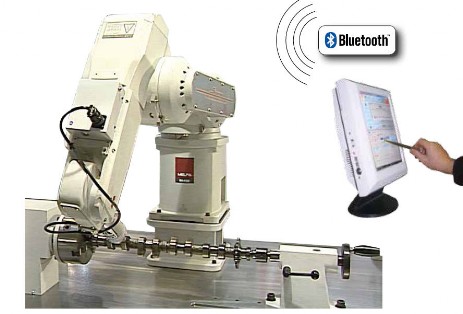
ARM
A hardness tester which represents the maximum automation applied to a hardness tester
Rockwell, Superficial Rockwell and Brinell / Test loads from 1 to 5,6 kgf (9,807 to 54,92 N)
This hardness tester's measuring head is anchored to a robotic arm which give you extreme mobility for accurate positioning on any area of the testing piece, especially on particular profiles that are normally difficult to measure.
Single or multiple tests on serial camshafts or any finished product.
The robotic arm rotatre on six different axis achieving a fully automatic system in order to decrease the time required for testing and increase productivity and precision.
The specific software used for the management of the robot offers quick setup of all test parameters and a complete set for analyzing the data received from the instrument.
It also has the abilities of graphic analysis, quick choice of testing scales, quick conversions, real time statistics and storage of testing sessions.
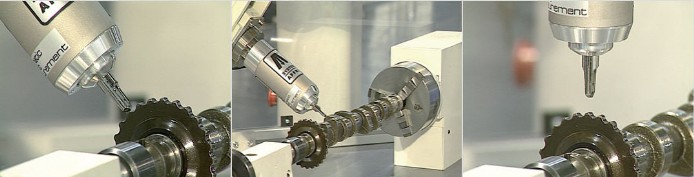
MRS FRU
Testing instrument for simultaneous measure of force and displacement
Traces the load displacement diagram and calculate the breaking point / Test loads from 1 to 100 kgf (9,807 to 980,7 N)
Real testing machine for compression and traction. It is fully motorized with closed loop load cell and can adapt to receive different clamping accessories for tensile, compression and breaking test.
The tester includes auto starting cycle using the key board or touch screen, software for test settings and statistics analysis and a large hard disk for data storage.
It is also possible to draw a customized test diagram of force or displacement.
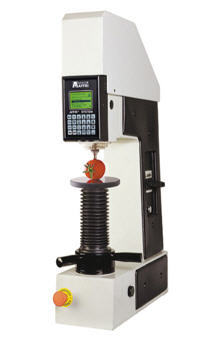
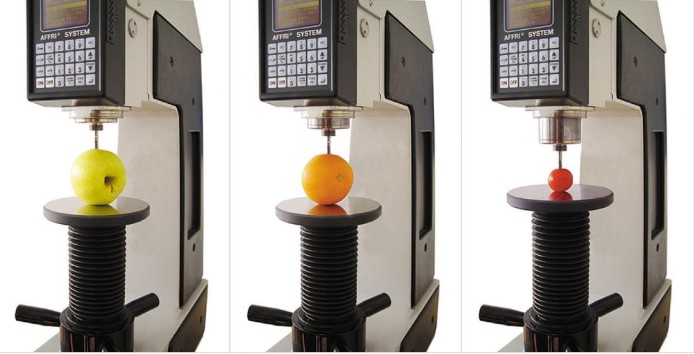