Testing procedures
Qualicoat > Qualicoat
2. Test Methods and Requirements
2.4.1 Dry adhesion2.4.2 Wet adhesion
2.5. Buchholz Indentation
2.6. Cupping test (only for the approval of organic coatings)
2.7. Bend test Model 266 S
2.8. Impact test
2.9. Resistance to humid atmospheres containing sulphur dioxide
2.11. Machu test
2.12. Accelerated weathering test
2.12.1 Accelerated weathering test for classes 1, 1.5 and 2 Cycle 1 (102 min dry/18 min wet)) (SOLARBOX E RH offers also immersion system).
After 1000 hours exposure the test panels shall be rinsed with demineralised water and checked for:
- Gloss variation: ISO 2813 - angle of incidence 60° & SPEKTROMASTER 565-D- Colour change: CIELAB Delta E*ab using the formula in ISO 11664-4, measurement including specular reflection. SPEKTROMASTER 565-D
2.13. Natural weathering test (Exposure in Florida according to ISO 2810) SPEKTROMASTER 565-D
2.14. Polymerisation test (Prescribed solvent for liquid coatings: MEK
2.15. Resistance to mortar
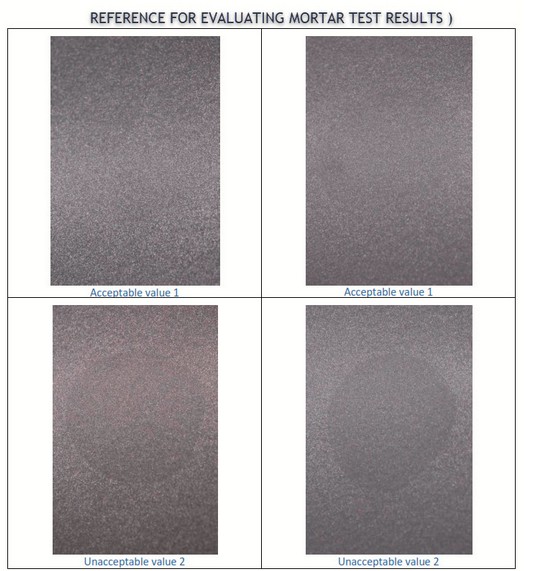
2.16. Resistance to boiling water
2.18. Sawing, milling and drilling (corrocutter)
2.19. Filiform corrosion test (Corrosion is produced by dripping hydrochloric acid) Model 463
2.21. Scratch and mar resistance test (Martindale) (gloss)
3. WORK SPECIFICATIONS
3.1. Storage of the products to be treated and layout of equipment
3.1.1 Storage
3.1.1 Layout of equipment
3.2. Surface preparation
3.2.1 Etching stage
Different types of etching are possible:▪ Type A : acid etching• Type A1: simple acid etching• Type A2: acid etching + acid etching▪ Type AA : dual etching• Type AA1: alkaline etching and acid etching• Type AA2: acid etching + alkaline etching + acid etchingThe etching degree is measured by taking the weight of a test sample before and after etching.Two preliminary pretreatments are defined:
a) Standard pretreatment (compulsory) The total etching degree shall be at least 1.0 g/m2 .b) Enhanced pretreatment (for SEASIDE endorsement) This pretreatment includes degreasing either in an independent step or in a combined degreasing/etching step.The total etching degree shall be at least 2.0 g/m2 . For type AA (dual etching) the two final steps shall be at least 0.5 g/m2.
3.3. Chemical conversion coatings
3.3.1 Chromate conversion coatings
Demineralised water shall be used for the final rinse after chemical chromate conversion before drying. (Beakers)The conductivity of the dripping water shall not exceed a maximum of 30 µS/cm at 20°C. The conductivity should only be measured for open sections and not for hollow sections. The weight of the chromate conversion coating shall be between 0.6 and 1.2 g/m² for chemical chromate conversion (yellow coating)and between 0.6 and 1.5 g/m² for chemical chromate-phosphate conversion (green coating).
3.3.2 Chemical pretreatments
The conductivity of the dripping water of all chemical pretreatment systems with a final rinse shall not exceed a maximum of 30 μS/cm at 20°C. (Beakers)
3.4. Anodic pretreatment (automatic SEASIDE endorsement)
The anodic pretreatment parameters can be as follows:
- Aluminium content: 5-15 g/lRecord of test results- Current density: 0.8-2.0 A/dm² - Agitation of the electrolyteCoating applicators using this type of anodic pretreatment shall perform and record the following additional tests:• Anodising bath
- The acid concentration and aluminium content of the anodising bath shall be analysed once per day.- The temperature of the anodising bath shall be checked every 8 hours.- The etching rate shall be checked once per day.- The thickness of the anodic coating shall be checked (every load).
• Testing of the coated finished products
- Before application, each coating (of a system and/or a manufacturer) shall be tested for resistance to boiling water, followed by an adhesion test (see § 2.4). - During application, resistance to boiling water shall be tested, followed by an adhesion test every 4 hours.
3.5. Electrophoretic coatings
The cleaned surfaces shall be rinsed in demineralised water with a maximum conductivity of 30 µS/cm at 20°C prior to coating.
3.6. Drying
After chemical pretreatment and before the application of organic coating, the products shall be dried thoroughly in an oven. For this purpose, a drying oven shall be installed in each plant.For continuous treatment9 the maximum drying temperature allowed is 100°C.For discontinuous treatment the products shall be dried at the following temperatures:
- chemical chromate conversion (yellow coating): maximum 65°C- chemical chromate-phosphate conversion (green coating): maximum 85°C
3.7. Coating and stoving
3.7.1 Coating3.7. 2 Stoving
The coating line shall have an oven for drying and one for curing; in cases where the oven is combined (performing both functions), an efficient control system for temperature and time shall be in place to ensure that suppliers’ recommended conditions can be followed.It should be possible to measure the temperature over the whole length of the oven.
3.8. Laboratory
The coating plant installation shall have laboratory facilities which are separate from the production facilities.The laboratory shall have the apparatus and chemicals necessary for testing and controlling the process solutions and finished products.The laboratory shall at least be equipped with the following apparatus:
3) 1 analytical balance (precision 0.1 mg)4) Cutting tools and instruments necessary for performing the adhesion test6) Recorder for stoving temperature and time with four different measuring points, three on the parts and one to measure the air temperature.8) Apparatus for testing resistance to cracking on bending9) Test solutions for the polymerisation test11) Device prescribed for the analytical coating weight determination (only for chemical pretreatment according to § 3.3.2)The conductivity of the dripping water of all chemical pretreatment systems with a final rinse shall not exceed a maximum of 30 μS/cm at 20°C.
Each piece of apparatus shall have a data sheet showing the apparatus identification number and calibration records.The oven temperature recorder shall be checked, and the results shall be registered at least twice per yea
3.9. In-house control
3.10. Operating Instructions
3.11. Registers
4. APPROVAL OF ORGANIC COATINGS
4.1. Granting of an approval
Any modification of the chemical properties of the binder (resin(s) and/or hardening agent(s) is tantamount to a new product and absolutely requires a new QUALICOAT approval
4.1.1 Technical information4.1.2 Minimum laboratory equipment
2) Instruments for measuring coating thickness4) Cutting tools and instruments necessary for performing the adhesion test5) Instrument for measuring indentation hardness6) Apparatus for cupping test8) Apparatus for controlling stoving temperature and time9) System for checking polymerisation11) Apparatus for accelerated weathering test1212) Light cabinet
4.1.3 Tests for granting an approval
Tests for granting an approvalThe following tests shall be made:
- Colour (2.1) SPEKTROMASTER 565-D- Gloss (2. 2)- Dry adhesion (2.4.1)- Indentation (2.5)- Cupping test (2.6)- Bend test (2.7) Model 266 S- Impact test (2.8) 11- Resistance to humid atmospheres (2.9)- Accelerated weathering test (2.12) + Gloss variation: ISO 2813 (angle of incidence 60°) & Colour change:- Polymerisation test (2.14)- Resistance to mortar (2.15)- Wet adhesion (2.4.2) Resistance to boiling waterNo blistering in excess of 2 (S2) according to ISO 4628-2.- Condensation water test (2.17)No blistering in excess of 2 (S2) according to ISO 4628-2
TEST METHODThe test shall be performed on one panel. The demineralised water shall be heated up to 60°C in a beaker of the proper size and kept under stirring to uniform temperature. The test panel shall be immersed for a half in water. Care must be taken not to put the panel in contact with the bottom of the beaker. The panel shall be immersed for 24 hours at 60 ± 1°C. The glass shall be properly covered to avoid water evaporation. At the end of the test, the panel shall be immediately cooled down in demineralised water at a temperature of ≤ 5°C. It shall then be dried with paper towels without rubbing. Colour change: Delta E and Delta L CIELAB formula according to ISO 11664-4, measurement including specular reflection.
- Scratch and mar resistance test Martindale (2.21)
REQUIREMENTS: Gloss retentionThe gloss retention shall be at least
• 60% for organic coatings with a structured appearance in all classes• 40% for class 1 and 1.5 smooth organic coatings• 30% for class 2 and 3 smooth organic coatings
- Natural weathering (Florida) (2.13)
REQUIREMENTS:
4.1.4 Basic colours to be tested for standard approvals and metallic extension
- Gloss
- Colour change SPEKTROMASTER 565-D
Classes 1, 1.5 and 2 The following colours shall be tested (independently of gloss category or appearance):
- white RAL 9010- blue RAL 5010- red RAL 3005
Class 3 The following RAL colours shall be tested:
• Lightness category LIGHT - RAL 1015 - RAL 7035 - RAL 9010• Lightness category MEDIUM - RAL 1011 - RAL 7040 - RAL 8024• Lightness category DARK - RAL 7016 - RAL 8019 - RAL 9005
4.1.4.2 Metallic extension
For all classes; if a manufacturer wishes to have an approval extended for metallic colours, tests shall be carried out on RAL 9006. RAL K5 glossy
4.1.5 Basic colours to be tested for special approvals
If a coating material is produced for a single colour, tests shall be carried out only on the colour mentioned in the system name. The tests are the same as those specified in § 4.1.3. No other colours may be produced under the same approval number.
4.1.5.1 Special approvals valid for single colours
4.1.6 Assessment of test resultsThe manufacturer shall send coating materials and coated samples to the laboratory in charge, together with the relevant technical data sheet for each colour. The data sheet shall include at least the following information: colour, gloss value and curing conditions (including range of times and temperatures). The testing laboratory shall prepare the test samples on its premises using chromium VIfree chemical pretreatment and the coating materials supplied by the manufacturer. The test samples may also be coated elsewhere provided that the inspector is present during the whole time of treatment. The testing laboratory shall always select the minimum stoving time and temperature specified by the manufacturer. After checking the colour and gloss, the laboratory shall perform the above-mentioned tests on the samples.
4.1.8 Inspection of coating manufacturer’s plantThe testing laboratory shall submit the test report to the General Licensee or to QUALICOAT in countries where there is no General Licensee.
A visit shall be required for new applicants in order to check the laboratory equipment of the coating manufacturer’s plant.
4.2. Renewal of an approval
4.2.1 Laboratory tests and Florida exposure4.2.1.1 Renewal of class 1 and class 1.5 approvals4.2.1.2 Renewal of class 2 and class 3 approvals4.2.1.3 Renewal of special approvals4.2.2 Sampling4.2.3 Assessment of laboratory test results4.2.4 Assessment of the Florida test results4.2.5 Banned colours
QUALICOAT shall publish on www.qualicoat.net the colours currently banned according to § 4.2.4, including colours suspended according to § 4.2.6, for every approved organic coating P-No. by the end of August. Banned colours shall not be used under QUALICOAT’s approval.
4.2.6 Suspended colours
A colour shall have the status “suspended” in case of:
• an unsatisfactory accelerated weathering test, with samples sent to Florida for the natural weathering test;• satisfactory results of the laboratory tests on a banned colour, with samples sent to Florida for the natural weathering test.
4.2.7 Withdrawal of an approval or extension4.2.8 Procedure for unbanning colour families for class 2
4.3. Powder manufacturer’s right of appeal
4.4. Use of the logo by coating manufacturers
5. LICENSING OF COATING APPLICATORS
5.1. Granting of a licence (quality label)
5.1.1 Inspection of materials5.1.2 Inspection of laboratory equipment5.1.3 nspection of production process and equipment5.1.4 Inspection of chemical pretreatment5.1.5Inspection of finished products
The inspector shall perform the following tests on the finished products:
- Appearance (to test the uniformity of production) (2.1)- Thickness (2.3)- Dry adhesion (2.4.1) and wet adhesion (2.4.2)- Acetic acid salt spray (2.10) (corrocutter)- Machu (2.11)- Polymerisation (2.14)- Sawing (2.18)
5.1.6 Inspection of the test panels5.1.7Review of in-house control and registers5.1.8 Final assessment for granting the licence5.1.9 “SEASIDE” endorsement
5.2. Routine inspections of licensees
The inspectors shall take along the following equipment:
- Thickness meter- Conductivity- Calibration tools for the other tests stipulated
5.3. Coating applicator’s right of appeal
5.4. Confidentiality of information
5.5. Deadlines for submission of inspection reports
5.6. Use of the logo by coating applicators
6. SPECIFICATIONS FOR IN-HOUSE CONTROL
The aim of in-house control is to give the coating plant a tool to keep control over its own production process.The number of shifts worked, the requirements, the results of the analyses and corrective actions shall be entered in charts or some other records/registration systems readily accessible to the inspector.The staff responsible for managing in-house control shall follow the training programme stipulated by QUALICOAT.
6.1 . Controlling the production process parameters
6.1.1Chemical pretreatment baths
The chemical parameters defined by the manufacturer of the chemical pretreatment materials shall be analysed at least once per bath in every working shift
6.1.2 Water quality
The conductivity of the final rinsing preceding chromate bath and of the demineralised rinsing water shall be measured at least once per bath in every working shift (Beakers)
6.1.3 Measuring the temperature of chemical pretreatment and rinsing baths
The temperature of the pretreatment baths and the final rinse, if a hot water rinse, shall be measured at least once per bath in every working shift,
6.1.4 Recording and measuring the drying temperature
The drying temperature displayed shall be recorded at least once in every working shift. The temperature should be measured on parts at least once a week using a recording instrument or some other means such as thermochromic pencils or tablets.
6.1.5 Measuring the stoving conditions
The stoving conditions according to § 3.7 shall be tested as follows:
• The displayed temperature shall be recorded at least once in every working shift.• A stoving curve shall be made on profiles at least twice a week.
6.2. Quality control of the chemical pretreatment
6.2.1 Testing the etching degree
The etching degree is measured by taking the weight of a test sample before and after etching.
6.2.2Testing the weight of the conversion coating
The weight of chromate conversion coating shall be tested in accordance with ISO 10546 at least once in every working shift
6.3. Quality control of the finished products
6.3.3 Appearance test
6.3.4 Adhesion test
6.3.4.1 Dry adhesion (ISO 2409)
The same panel to be chosen for dry adhesion test, bend test and impact test.
6.3.4.2 Wet adhesion
6.4.1 Control register for the production process6.4.2 Control register for test panels
This control register is either a bound register (not a spiral binding) with numbered pages, or a computer listing. It shall show the following information:
- the production date- the references of the organic coating material used: RAL or some other reference for identification, lot number, manufacturer's name
- the following results:
- gloss test- thickness test- adhesion test- polymerisation test (optional for powder coatings)- bend test Model 266 S- impact test- colour shade inspection (visual inspection to compare the actual colour with the colour shade required by the customer) SPEKTROMASTER 565-D
6.4.3 Control register for finished products
It is either a bound register (not a spiral binding) with numbered pages, or a computer listing.It shall show the following information
- the customer's name and the order or lot identification data- the production date- the reference of the organic coating material used- the following results:- coating thickness test (minimum and maximum values)
6.4.4 Control register for tests carried out by the chemical manufacturer
This is either a bound register (not a spiral binding) with numbered pages, or a computer listing.It shall show the following information- sample reference
- date of sampling and dispatch/collect- chemical manufacturer’s test report- test results (see Appendix A6)- remarks and/or corrective action.
6.5. Table summarising the specifications for In-House Control .
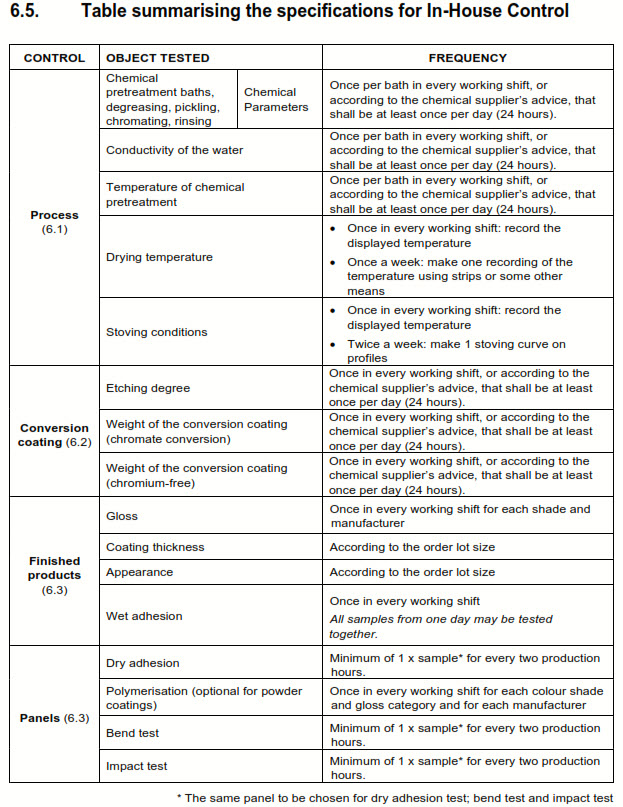