Cathodic Delaminator
Coatings & Industry > CORROSION > Corrosion Quick Test
Cathodic Delaminator, Model 602
The Cathodic Delaminator, Model 602, is used for rapid checking of product quality and frequently quality control of coated metals.
The apparatus consists of a control unit and a temperature control vessel (immersion container) with 8 test receptacles and circulator.
Each test vessel has its own constant current source.
So you can use up to 8 specimen for testing, independently of each other.
The cathodic delamination allows the determination of infiltration of the coating in the damaged area and erroneous pretreatments can be made visible (formation of bubbles during pinholes, scratches or stone impact).
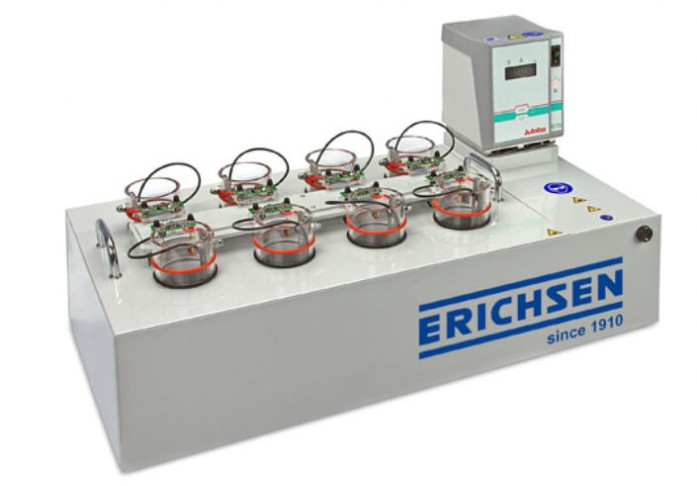
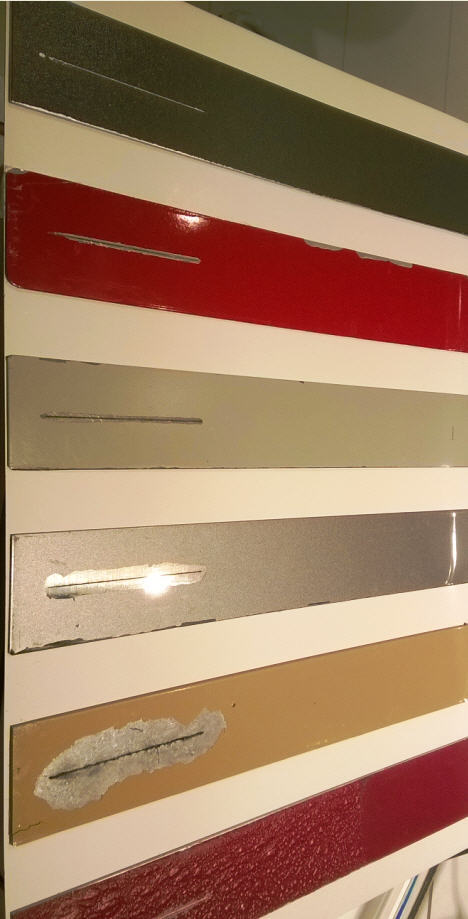
Purpose and Application
Mechanical injury of organic coatings on metal cause the loss of corrosion protection.
Known examples of the mechanical destruction of coatings are : stone impact on motor vehicles, transport and installation damage.
Corrosion will be affected by corrosion protection system.
Particularly the preparation of the substrate surface before coating and the composition of the coating are important for corrosion protection systems.
The Cathodic Delaminator, Model 602, is used for rapid checking of product quality and frequently quality control of coated metals.
The apparatus consists of a control unit and a temperature control vessel (immersion container) with 8 test receptacles and circulator.
Each test vessel has its own constant current source.
So you can use up to 8 specimen for testing, independently of each other.
Principle of the Test
Test instrument for examining the corrosion of coated metals.
With a scratch tool (e.g. Scratching Tool acc. to van Laar, Model 426) the protective layer will defined injured by a 5 cm long scratch, through to the metallic specimen.
The specimen is placed in a test receptacle filled with electrolyte (0.5 N KOH) and will then secured with an alligator clip.
The test will started by a timer (test duration 30 min).
The corrosion can now be observed under the accelerated conditions.
After the test, the samples are rinsed with water and dried.
The infiltrated surface coating will removed with a knife or scalpel.
The cathodic delamination allows the determination of infiltration of the coating in the damaged area and erroneous pretreatments can be made visible (formation of bubbles during pinholes, scratches or stone impact).
Technical Data
Dimensions (L x W x H)
Immersion test container approx. 700 x 350 x 352 mmSupply unit approx. 260 x 275 x 110 mm
Power supply 230 V AC, 50 Hz
only for operating in IT network with a residual current circuit breaker 30mA
Weight (net)
Supply unit approx. 3 kg
Immersion container with test receptacles approx. 12.5 kg
Immersion container with test receptacles and temperature control vessel with circulation approx. 16 kg
Heating period
Test receptacles approx. 20 min.Enviroment temperature 23 C°Water temperature 20 C°
Heating period with Immersion container approx. 1.5 hours
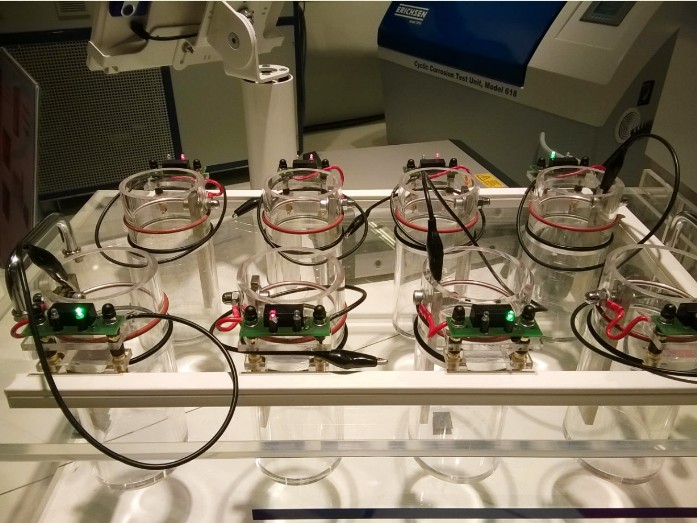
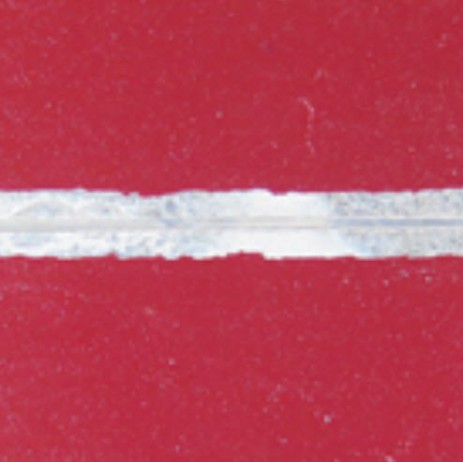
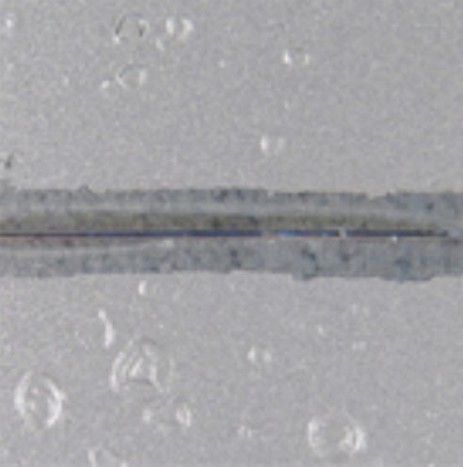