TABER® ABRASER 352 S - Typ 1700
Coatings & Industry > Mechanical properties > Abrasion & Washability
TABER® ABRASER 352 S (type 1700)
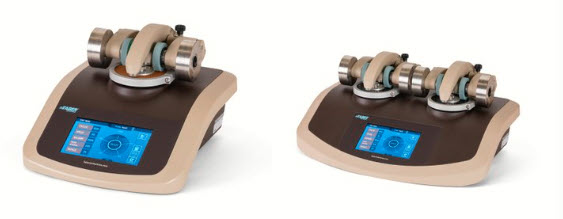
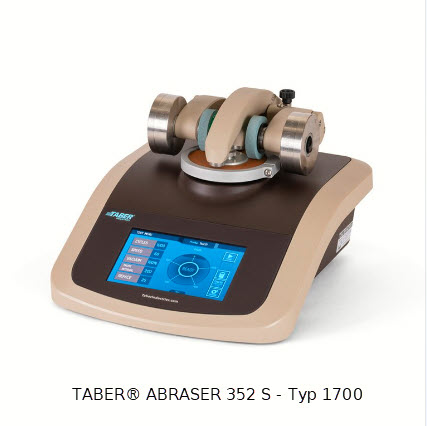
TABER® ABRASER 352 S - Typ 1700
The TABER® ABRASER 352 S (Platform), with its attractive and modern design, is a robust tabletop unit.
The precise control and drive elements are located in a sturdy aluminium housing.
Easy operation is via LCD touch screen, with functions such as abraser status, visual reference of completed test, cycle/time switching (completed or remaining), programmable pause interval, language selection and much more.
The TABER® ABRASER Model 352 S (Type 1700) has one specimen holder for performing abrasion tests.
“Taber Test” delivers reliable data in minutes.
Used to evaluate a material’s resistance to wear, a flat
specimen is mounted to a turntable platform that rotates on a vertical axis. As the turntable rotates, contact
of the specimen against the sliding rotation of two abrading wheels cause wear while a vacuum system
removes loose wear debris during the test.
The resulting abrasion marks form a pattern of crossed arcs in
a circular band that cover an area approximately 30 cm2
.
Purpose and application:
Resistance to abrasion is one of the most important mechanical properties of surfaces.
Among the methods used to test abrasion resistance, working with the TABER® ABRASER is the most common and widely used method.
Numerous national and international standards make explicit reference to this test instrument.
The Original TABER® ABRASER can be used to perform abrasion tests on paintwork and other coatings, such as rubber, paper, leather, ceramics, textile fabrics and metals.
This device is used in research and development as well as in production and quality control.
Principle of the test:
The abrasion is caused by two friction rollers which act with a defined force on the rotating specimen holder to which the specimen is attached.
An essential feature of these abrasion tests is the X-shaped grid.
The abrasion behaviour can be determined by the following test methods:
- Weight loss method: The material to be tested is subjected to a defined number of cycles of revolution.
- Visual final test method: The sample is exposed to abrasion until the sample surface becomes visible.
- Abrasion depth determination: After a specified number of cycles, the abrasion depth is measured with the aid of a micrometer
Scope of delivery:
- Taber ABRASER 352 S (Type 1700)
- Attachable weights (1000 g load) - 2 pcs
- Attachable weights (500 g load) - 2 pcs
- Specimen holder (pre-assembled) - 1 pc.
- Coupling ring for sample holder - 1 pc
- Torx T25 screwdriver for tightening the
Cap rings - 1 pc. - Brush for cleaning samples - 1 pc.
- Vacuum cleaner with suction brush and hose - 1 pc.
- Power cable 115/230 VAC
- Operating instructions
Norms
- EN 13329
- NEMA LD 3-2000
- EN 438-2
- ISO 4586-2
- NALFA LF-01
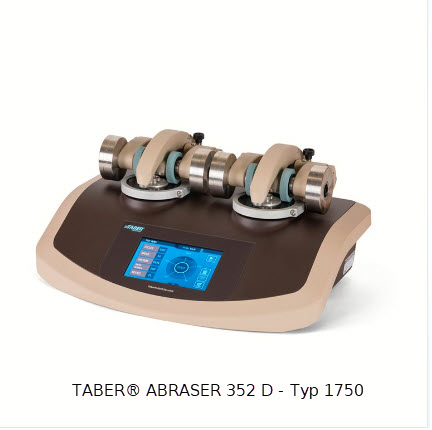
TABER® ABRASER 352 D - Typ 1750
The TABER® ABRASER 352 D (Platform), with its attractive and modern design, is a robust tabletop unit.
The precise control and drive elements are located in a sturdy aluminium housing.
Easy operation is via LCD touch screen, with functions such as abraser status, visual reference of completed test, cycle/time switching (completed or remaining), programmable pause interval, language selection and much more.
The TABER® ABRASER Model 352 D (Type 1750) has two specimen holders for performing abrasion tests.
Purpose and application:
Resistance to abrasion is one of the most important mechanical properties of surfaces.
Among the methods used to test abrasion resistance, working with the TABER® ABRASER is the most common and widely used method.
Numerous national and international standards make explicit reference to this test instrument.
The Original TABER® ABRASER can be used to perform abrasion tests on paintwork and other coatings, such as rubber, paper, leather, ceramics, textile fabrics and metals.
This device is used in research and development as well as in production and quality control.
Principle of the test:
The abrasion is caused by two friction rollers which act with a defined force on the rotating specimen holder to which the specimen is attached.
An essential feature of these abrasion tests is the X-shaped grid.
The abrasion behaviour can be determined by the following test methods:
- Weight loss method: The material to be tested is subjected to a defined number of cycles of revolution.
- Visual final test method: The sample is exposed to abrasion until the sample surface becomes visible.
- Abrasion depth determination: After a specified number of cycles, the abrasion depth is measured with the aid of a micrometer
Scope of delivery:
- Taber ABRASER 352 D (Type 1750)
- Attachable weights (1000 g load) - 4 pcs
- Attachable weights (500 g load) - 4 pcs
- Specimen holder (pre-assembled) - 2 pcs
- Coupling ring for sample holder - 2 pcs
- Torx T25 screwdriver for tightening the Cap rings - 1 pc.
- Brush for cleaning samples - 1 pc.
- Vacuum cleaner with suction brush and hose - 1 pc.
- Power cable 115/230 VAC
- Operating instructions
Norms
- EN 13329
- NEMA LD 3-2000
- EN 438-2
- ISO 4586-2
- NALFA LF-01
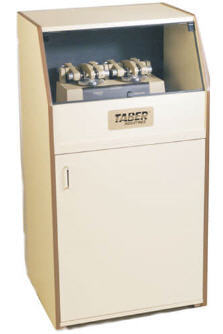
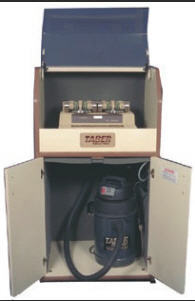
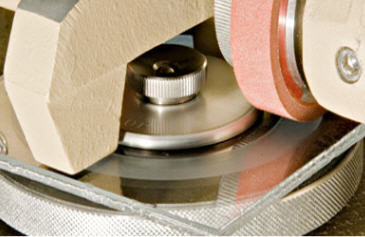
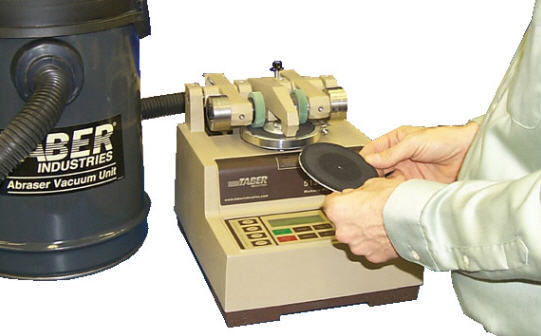
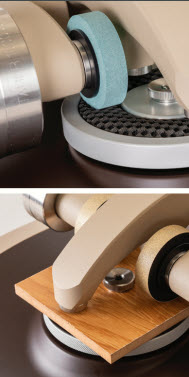
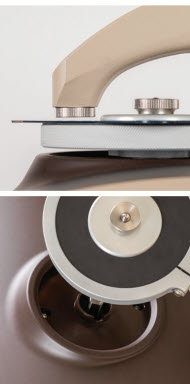
Evaluation
There are various techniques used to interpret results generated with the TABER Rotary Platform Abraser (Abrader). The method of evaluation that you select should reflect the type of material that is being tested. If you are following a specification - the method for interpreting test results will be listed.
The most common methods of evaluating results from the Taber Abraser (Abrader) include:
Cycles to a Specific End-Point - The number of cycles required to reach a predetermined end point, or the appearance or condition of the specimen after a fixed number of cycles. The evaluation criteria may include: loss in breaking strength, yarn breakage, loss in coating, change in gloss, color loss, or other changes in appearance. In these cases, the abraded sample is usually compared to a known standard of the material tested. When visually inspecting changes in specimen appearance, evaluations should be made using an agreed upon rating system such as a visual grading scale (e.g. five-step) or pass/fail criteria.
Weight (Mass) Loss - This technique measures how much material has been removed by abrasion, and is usually reported in milligrams.
L = A - B
where L = weight loss
A = weight (mass) of specimen before abrasion
B = weight (mass) of specimen after abrasion
When performing the weight loss method, loose particulate may adhere to specimens during testing. It is critical that you clean off the test specimens as best as possible prior to weighing.
Taber Wear Index - Indicates rate of wear, and is calculated by measuring the loss in weight (in milligrams) per thousand cycles of abrasion. The lower the wear index, the better the abrasion resistance.
I = [(A - B) * 1000] / C
where I = wear index
A = weight (mass) of specimen before abrasion
B = weight (mass) of specimen after abrasion
C = number of test cycles
Volume Loss - When comparing the wear resistance of materials that have different specific gravities, a correction for the specific gravity of each material should be applied to give a true measure of the comparative wear resistance. Calculate the wear index as shown above, and divide the result by the material's specific gravity. The use of this correction factor provides a wear index related to the loss in volume of the material to which it is applied. When comparing materials of different specific gravities, test parameters must be the same including wheel selection and load.
Wear Cycles Per Mil (0.001 inch) - Used to express abrasion cycles required to wear through a coating of a known thickness.
W = D / T
Where W = Wear Cycles Per Mil
D = number of cycles required to wear coating through to substrate
T = coating thickness, mils
Depth of Wear - To determine the depth of wear, use a thickness gauge or other appropriate device to measure the specimen thickness on four points along the path to be abraded, approximately 38 mm from the center hole and 90° apart. Calculate the average of the readings. After subjecting the specimen to abrasion, repeat the measurements and average the readings. Calculate the difference. Alternatively, the depth of the wear can be measured with an instrument such as an Optical Micrometer.
Residual Breaking Force (textile fabrics) - This technique measures the effective strength of the fabric, or force required to break a specific width of fabric. To determine the individual breaking force of the abraded specimen use the procedure described in the ASTM D5034 and D5035 Standard Test Method for Breaking Strength and Elongation of Textile Fabrics. [Note, you must change the referenced distance between clamps to 25mm and horizontally place the path of abrasion on the abraded specimen midway between the clamps.] Report the breaking load to the nearest 0.5kg.
Average Breaking Strength (textile fabrics) - Calculated by averaging the breaking strength of the abraded specimens and the unabraded specimens, as determined by the Residual Breaking Force.
Percentage Loss in Breaking Strength (textile fabrics) - To determine the breaking load of the original fabric and the abraded specimen, use the procedure noted above (ASTM D5034 and D5035). Calculate the percentage loss in breaking strength to the nearest 1% for each lengthwise and widthwise directions.
AR% = 100 * (X - Y) / X
where AR% = abrasion resistance, %
X = breaking force before abrasion, g (lb)
Y = breaking force after abrasion, g (lb)
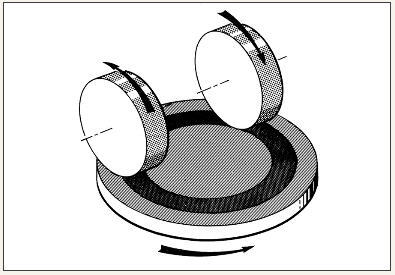
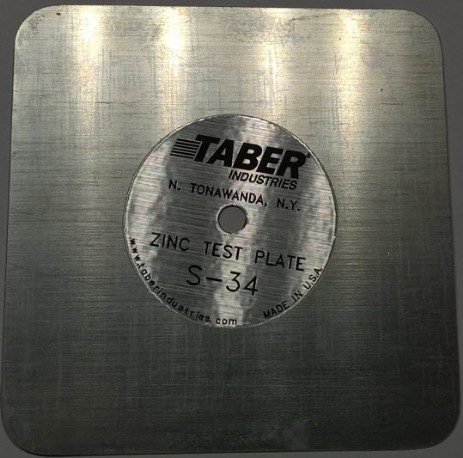
A c c e s s o r i e s
Art.-No. Description
101-03524652 Quiet Cabinet, complete set (136134-230)
101-17000152 Wheel Refacer, Model 350
101-17000252 Single Point Diamond Tool (133-60) for Model 350
101-17000352 Multiple Point Diamond Tool (200-62) for Model 350
101-17003052 TABER® Grit Feeder 355 (980355)
101-03525652 Rotary Abraser Calibration Verification Kit
101-03525752 Wheel tracking cards S-45 per 15 pcs.
101-03526852 CALIBRASE wheels CS-8, purple, resilient, extra fine abrasion, per pair
101-03521752 CALIBRASE wheels CS-10F, brown, resilient, fine abrasion, per pair
101-03520753 CALIBRASE wheels CS-10, green, resilient, medium abrasion, per pair
101-03526052 CALIBRASE wheels CS-10W, white, resilient, medium abrasion, per pair
101-17000452 CALIBRASE wheels CS-10P, green, resilient, medium abrasion, per pair
101-03521852 CALIBRASE wheels CS-17, green, coarse abrasion, per pair
101-03526652 CALIBRASE wheels CS-T3 per pair red, resilient, fine abrasion (corresponds to old version of wheels CS-10F, type III)
101-03522052 CALIBRADE wheels H-10, grey, vitrified, sintered, fine grain, fine abrasion, per pair
101-03520853 CALIBRADE wheels H-18 grey, vitrified, sintered,medium grain,medium abrasion, per pair
101-03522152 CALIBRADE wheels H-22 grey, vitrified, sintered, coarse grain, coarse abrasion per pair
101-03522252 CALIBRADE wheels H-38, tan, vitrified, sintered, fine grain, very fine abrasion, per pair
101-03524452 Sandpaper strips S-33, self-adhesive, acc. to EN 438-2, ISO 4586-2, DIN 53 799 NEMA LD 3,
for abrasion wheels S-32, per 100 pcs
101-03526252 Sandpaper strips S-33, self-adhesive, acc. to EN 438-2, ISO 4586-2, DIN 53 799, NEMA LD 3,
for abrasion wheels S-32, per 500 pcs.
101-03524352 Sandpaper strips S-42, self-adhesive, for abrasion wheels S-32, per 100 pcs
101-03525552 Sandpaper strips S-42, self-adhesive, for abrasion wheels S-32, per 500 pcs
101-03521452 Rubber wheels S-32/CS-0 for sandpaper strips S-33/S-42 per pair
101-03521552 Felt wheels CS-5, resilient, white, no abrasive, per pair
101-650000341 Felt strips, self-adhesive, for tests acc. to DIN 68 861, Part 3 (behaviour when wiping furniture surfaces)
for application on abrasion wheel CS-0, per 50 pcs.
101-03521152 Tungsten CARBIDE wheels S-35 per pair
101-03521753 Leather wheels S-39 (per pair)
101-17000552 Aluminium Wheel Set S-24 (per pair)
101-03520553 Abrasive discs S-11 for refacing CALIBRASE wheels per 100 pcs
101-03526752 Testing disc ST-11 „Refacing Stone - Fine“
101-03521252 Specimen mounting cards S-36
101-03524952 Specimen mounting cards S-36-1
101-03521352 Specimen mounting sheets S-37 (100 pcs./pkg.)
101-03524752 Specimen mounting sheets S-37-1 (100 pcs./pkg.)
101-03520453 Specimen plates S-16, material: steel (10pces/pkg)
101-17000652 Specimen Plates (birch plywood) S-17 (per 10 pcs.)
101-17000752 Specimen plates of Aluminium S-18 (per 10 pcs.)
101-03520552 NEMA glass standardization plates S-31 per 10 pcs
101-03520852 Standardization plates S-34, material: zinc, per 5 pcs
101-03521653 Standardization plates S-38, 4 x 4', ¼'-hole (per 10 pcs)
101-03522352 Rubber pads S-19 for specimen holder, O.D. 10,8 cm (5 pcs./pkg.)
101-03522452 Extension nut S-21, for rigid specimens (6.3 to 12.7 mm thick) (¼' to ½')
(requires a 9.52 mm (3/8')hole in the specimen)
101-17001052 Specimen holder 'Standard' SH-125 complete with rubber pad, nut an clamp plate
101-17001152 Specimen hold-down ring 'A' SH-101, for flexible materials up to 0.79 mm thick, incl. TORX T25 screwdriver
101-17001252 Specimen hold-down ring 'B' SH-102, for flexible materials up to 1.59 mm thick, incl. TORX T254 screwdriver
101-17001352 Specimen holder (tall) SH-12, complete with rubber pad, nut and clamp plate
101-17001452 Specimen holder 'Textile' SH-15, complete with rubber pad, nut and clamp plate
101-17001552 Specimen holder 'Drive Pin' SH-19, incl. TORX T25 L-key
101-17001652 Specimen 'Sliding Mount' SH-26, incl. TORX T25 L-key
101-17001752 Specimen holder SH-75 - rimmed
101-17001852 Arm Height Extension Kit (1700-40) for test specimens up to 40 mm
101-17002352 Wheel tracking cards S-45/2 (132150-2) 15 pcs
101-17001952 Counterweight Set 50 g 'Arm Kit' (135369) to achieve 125 g load (2 pcs.)
101-17002052 Counterweight-Set 125 g (135937), for Counterweight Set 'Arm Kit' (Ord.-No. 17001952)
101-17002152 Counterweight-Set 150 g (135927), for Counterweight Set 'Arm Kit' (Ord.-No. 17001952)
101-17002252 Counterweight-Set 175 g (135928), for Counterweight Set 'Arm Kit' (Ord.-No. 17001952)
101-03520653 Brush S-12 for cleaning specimen plates
101-17003152 Vacuum cleaner ELSEA (230 V, 50 Hz) (136094) incl. flexible suction hose and round brush
101-17003252 Vacuum cleaner ELSEA (115 V, 60 Hz) (136093) incl. flexible suction hose and round brush
101-17003352 Paper Filter Bag ELSEA (FI003C/10) - 20 lt. per pc.
101-17003452 Polyester Filter Bag ELSEA (FI003P/5) - 20 lt, per pc.
101-03524852 Sample cutter '5000' (985000), O.D. 4.2' (107 mm) with a centrical hole with an outer diameter of ¼' (6 mm)
101-17002452 'Scuffing Head' Attachment SH-300 (135647) incl. two load auxiliary weights (1 lb and 2 lb),
TORX T10 L-key; without scuffing heads
101-17002552 Scuffing Head, type 'A' (135636) for Ford Motor Company Physical Test Method FLTM BN 108-04 '
Resistance to scuffing' or SAE J365, to use with 'Scuff'-Attachment SH-300.
101-17002652 Scuffing Head, type 'B' (135637) for General Motors GM9911P; to use with 'Scuff'-Attachment SH-300.
101-17002852 Auxiliary weight (453 g /1 lb) for 'Scuff'-Attachment SH-300
101-17002952 Auxiliary weight (907 g /2 lb) for 'Scuff'-Attachment SH-300
101-03521853 Grit S-41, 50 pound container (1 pound = 453,6 g)
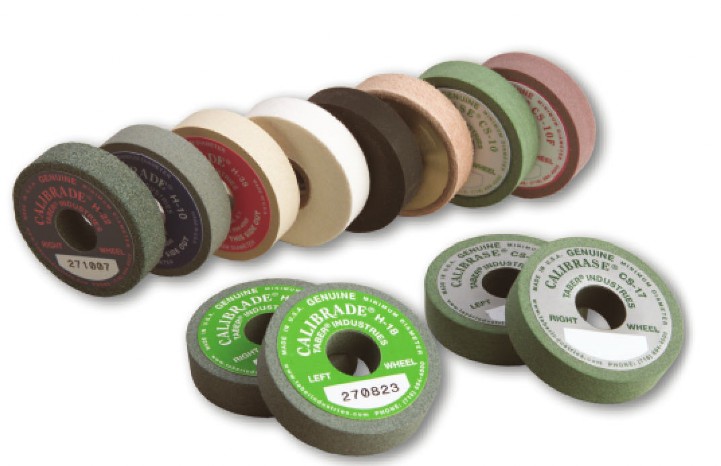
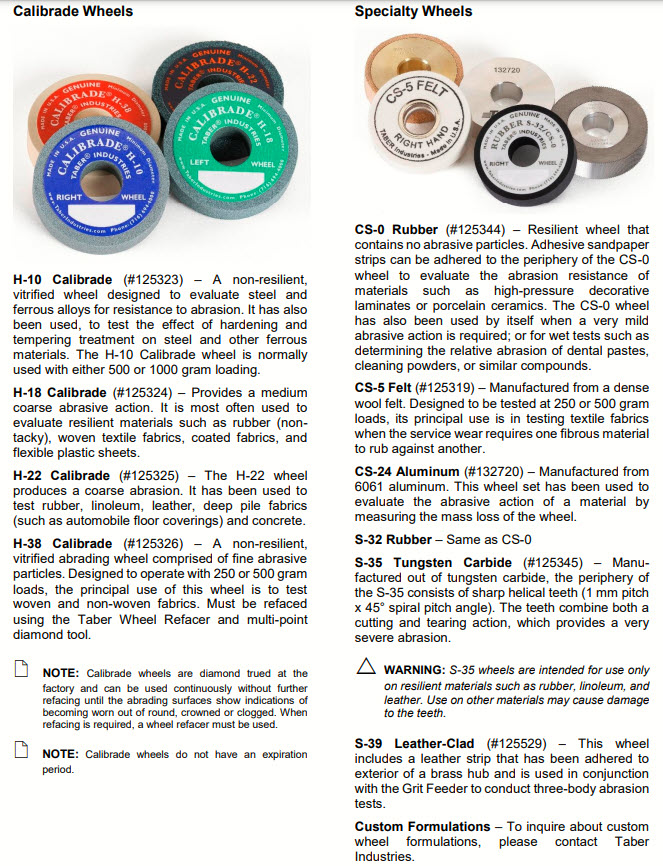
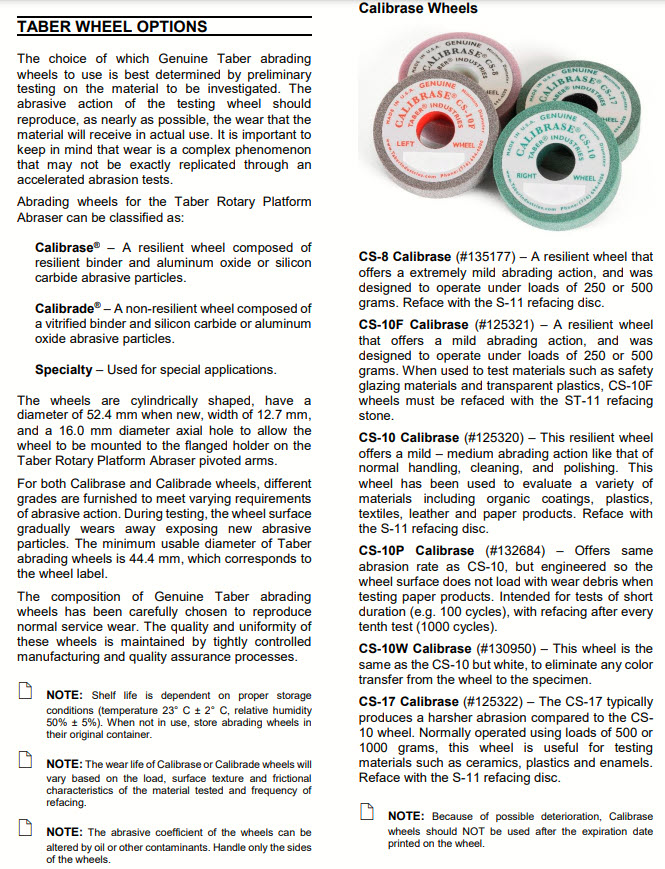
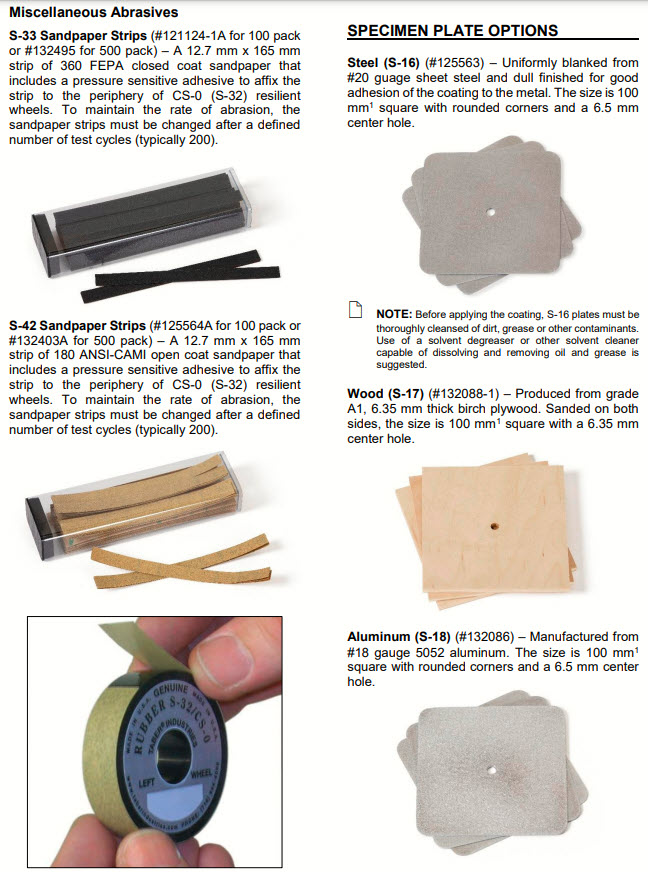
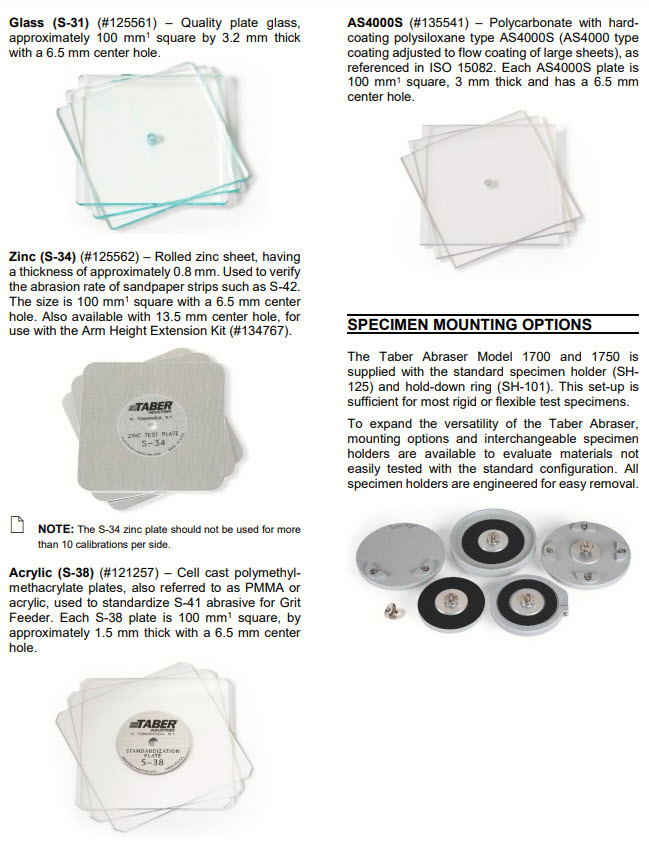
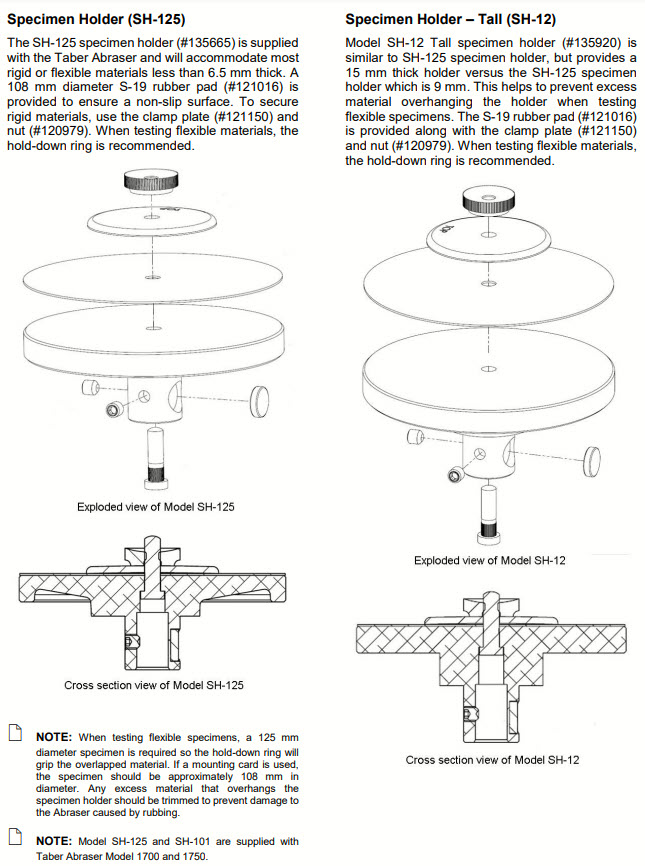
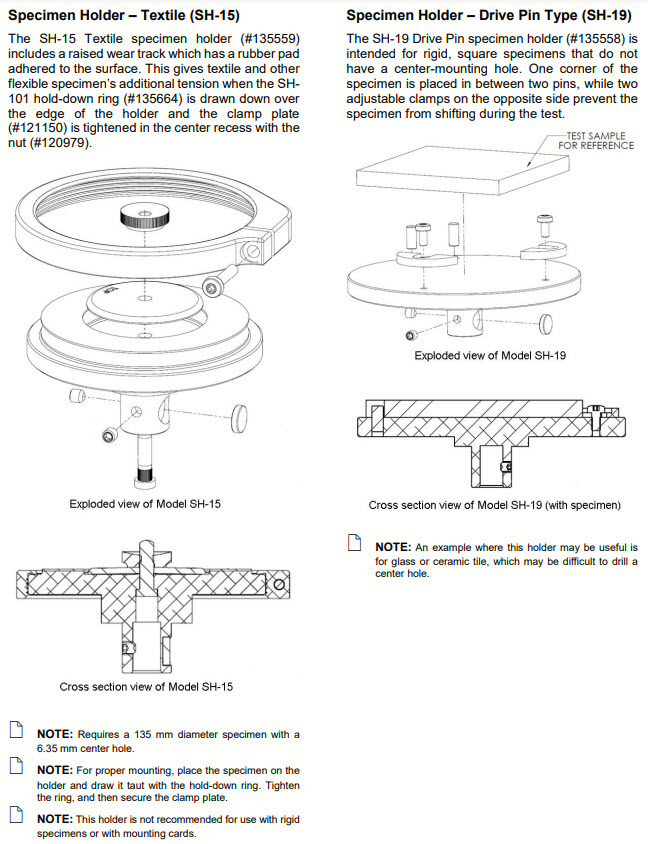

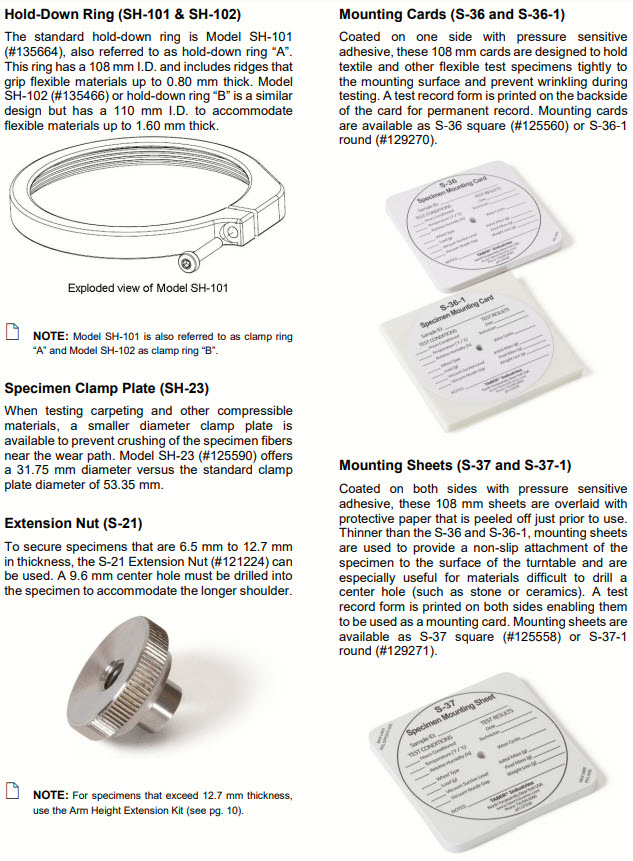
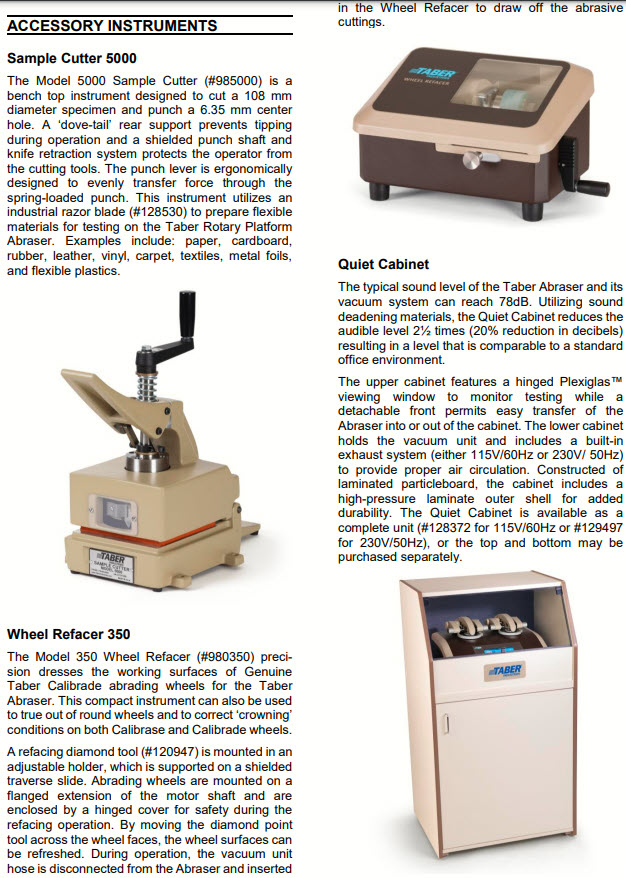
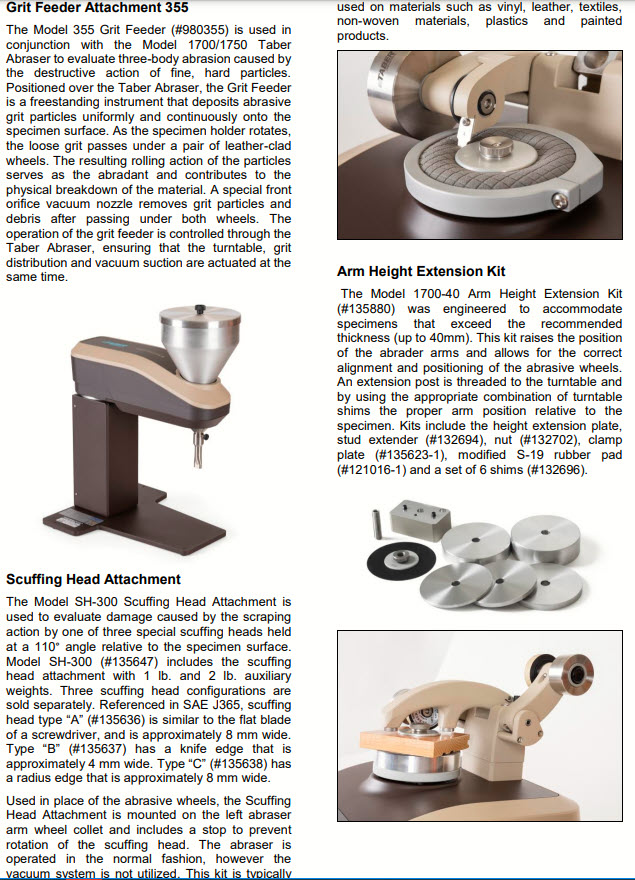
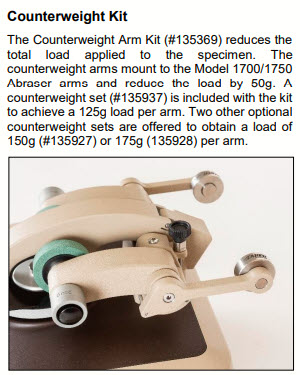
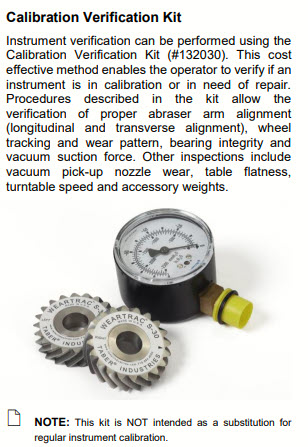