Gradient Oven
Coatings & Industry > Physical properties > Drying Time
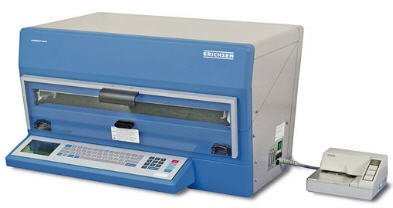
Gradient-oven, Model 432/I
- Efficient measurement of temperature-dependent properties
- Simulation of industrial stoving processes with programmable gradients
For evalution the baking and drying behavior of liquid coatings, powder coatings, resins, plastics, etc., with an operating temperature of 30 °C to 250 °C, operation and controlling via built-in alphanumeric keypad (menu-guided English, French or German), three interfaces (controlling a printer, output date to a PC, connecting an oven temperature recorder/data logger), built-in software for connecting a data logger, safety protective shutter.
2 versions available : 30 – 250 °C & 30 – 320 °C
To assess the drying and baking behaviour
To assess the resistance of chemicals
The scope of suppy includes:
- Glass plate made of special glass
- Exhaust tube
- Test panels made of steel (25 pcs.)
- Marking strips (50 pcs./ 25 pcs. each numbers/blanko)
- Operating manual.
- Power supply: 230 V, 50/60 Hz, 3400 VA
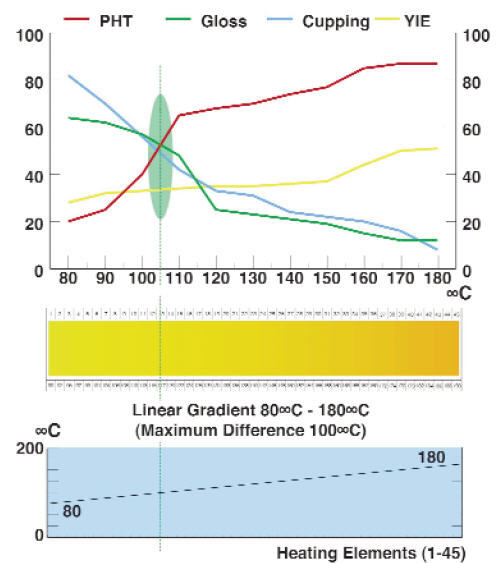
Purpose and Application
Acid rain, bird droppings, fuel, antifreeze and many other environmental factors can damage automotive finishes. Especially in summertime, some substances can be very aggressive and cause severe damage. Therefore, automotive paint manufacturers as well as auto makers need to find out how different environmental phenomena will interact with a coating system.
For the development of stove enamel systems as well as for their quality testing it is of great importance to assess the temperature range and the max. temperature limit, respectively, where the components of the lacquer formulations (and thus also potentially the properties and the quality of the whole thing) begin to change.
The well-known main example for this are the yellowing of binding agents as well as the change in colour of pigments.
Concerning the subject of baked coatings within industrial production conditions, the accurate control of the corresponding processes is of crucial importance to achieve and continuously maintain/ guarantee the specified qualitative characteristics of the coating.
Due to different reasons, the actually existing conditions do not always correspond exactly to the preset process run which in the “worst case“ may cause severely high non-conformity costs.
The Gradient-oven 432 offers the possibility of a needs-based optimizing of the process for the product in question.
The „actual condition“ in the stove enameling production line, beforehand determined by means of an oven temperature recorder, can be simulated at the best via a requirement-orientated setting of an appropriate gradient and thus allows a nearly perfect 1:1 simulation of the respective stoving condition, however on the desired laboratory scale saving time and expenses.
Principle of the Test 1
The Gradient-oven, Model 432, is a testing instrument for the assessment of the baking and drying behaviour of paint and powder coatings, resins, plastic materials and similar. The production process can be simulated by programming heat-up speed, baking temperature, and time.
The gradient-oven helps to speed up R & D projects saving time and money. The very good repeatability of measurements allows a
remarkably accurate determination of the present limiting values.
Depending on the gradient-oven type coatings can be tested with temperatures up to 320 °C. By applying the coating system with a duplex frame applicator two different coating systems can be applied simultaneously on the same panel. This makes the comparison easier saving application time and material cost. In QC testing of baked coating systems the gradient-oven produces repeatable results many times faster than using traditional convection ovens.
In a standard test 5 different chemicals can be tested on one panel – e.g. H2SO4 which simulates atmosphere and acid rain, NaOH for car wash detergents, pancreatine (bird dropping), brake fluid, and tree resin.
Liquid paints are applied with a film applicator and film application device. It is also possible to apply them by spraying, once the edges and reverse of the test panel have been masked. Powder coatings are applied electrostatically to either masked panels or panels covered with a magnetic strip. The panels are coated and baked under the specified processing conditions.
Using a pipette droplets (approx. 0.05 ml) of these various materials are placed at appropriate intervals on the test panel. Repeat this length down the panel with spacing about every 2 - 3 cm.
Principle of the Test 2
For evaluation the panels are thermally stressed and then washed under running water, dried and visually evaluated. The evaluation should be done after approx. one hour and again after 24 hours to see if any additional etching has occurred.
The temperature is documented at which the first visual changes and damages occurred.
The Gradient-oven, Model 432, is equipped with a microprocessor-controlled heating bench with 45 isolated heating elements, which produces a completely linear temperature gradient or step gradient.
"Linear gradient“: means that a constant temperature is generated over the entire test panel. The linear gradient can be horizontal, i.e. the same temperature on both right and left sides of the test panel. However, a temperature can also be generated that is low on the left and high on the right with a maximum increase of 100 °C.
“Step gradient”: 3 steps are offered to automatically divide the test panel into 2, 3 or 4 equal parts (temperature steps). Between each temperature step some heating elements are not heated to maintain the set value of each step. These elements are indicated in the report or the set temperature display at 23 °C.
Execution
The Gradient-oven, Model 432, is a laboratory tabletop instrument, which can be placed in a nonhazardous area/room with normal room temperature (approx. 18 °C to 25 °C) and humidity (approx. <85%).
The operation and controlling are menu-guided in English, French or German only via the built-in alphanumeric keypad. All retrievable functions are displayed in the appropriate menu on the display.
The gradient-oven has three interfaces. Two of them are permanently activated to actuate a printer and to transmit data to a PC. The third interface is used by the communication device when connecting an oven temperature recorder/data logger. The software needed for this is already "on board". The scope of supply includes a special glass plate to insulate the area between the heating elements and test panel as well as particularly specified test panels.
In front of the opening a front shutter was added, which, for safety reasons, has to be in the closed position while the panel holder carriage is moving before and after the heating phase.
The gradient-oven conforms to Safety Class 1. All ovens are subject to an extensive quality control in accordance with DIN VDE 0700 Part 1. 70
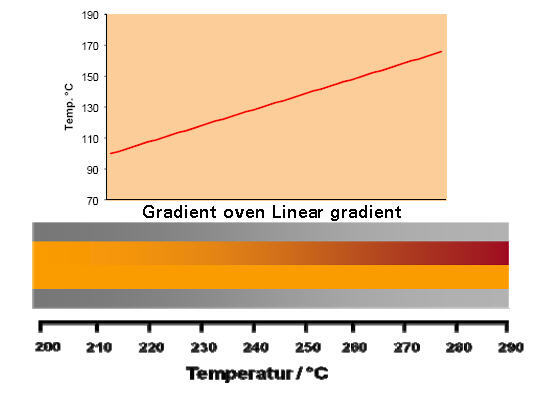
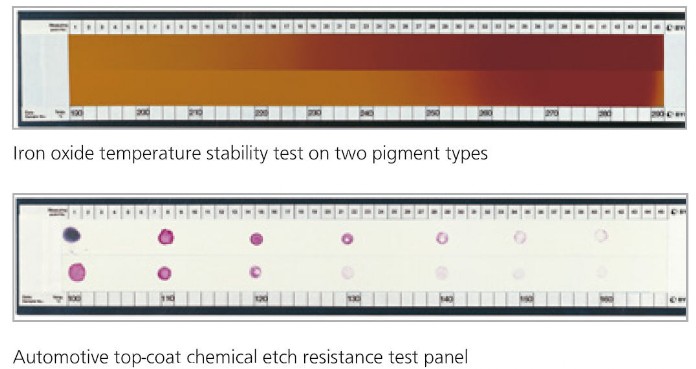
Technical Data
Voltage : 230 V, 50/60 Hz
Power Consumption : 3400 VA
Heating Surface : 520 x 100 mm
Test Surface : 500 x 70 mm
Heating Elements : 45 pcs.
Pressure Platform : reciprocates automatically (16 kp) for insertion and removal of panel
Linear Gradient : max. temp. difference between 30 and 250 (320) °C: 100 °C;
Step Gradient : with 2, 3 or 4 steps: max. temp. difference between two steps: 50 °C
Heat-Up-Speed : 2 °C to 30 °C/min, programmable
Baking Time : in sec. and min.
Memory max. : 10 gradients
Accuracy control accuracy of the heating elements: < ± 2 °C surface temperatures on 0.8 mm test panels from element 3 up to 43:
to 200 ° ± 2 °Cto 250 ° ± 3 °Cto 320 ° ± 5 °C
measured under specified test conditions
Dimensions : 465 x 720 x 595 mm
Weight : 50 kg
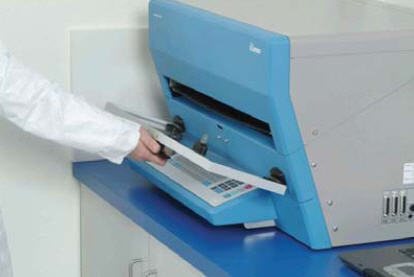
PANELS FOR GRADIENT OVEN
Carbon steel and aluminium panels for Gradient Ovens.
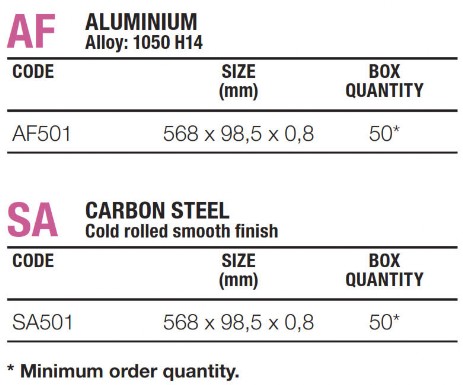
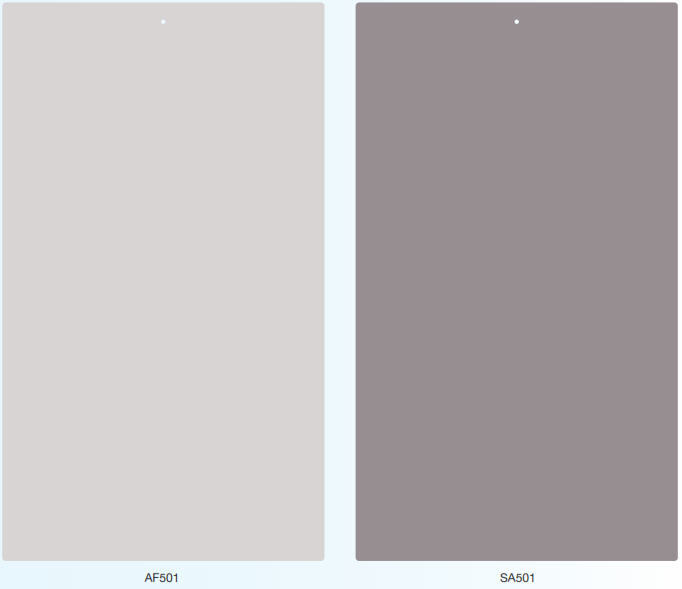