Impact
Coatings & Industry > Mechanical properties > Flexibility and toughness
Various standardized versions
Each version can be upgraded with various test sets
ASTM D 2794
ISO 6272-1
ISO 6272-2
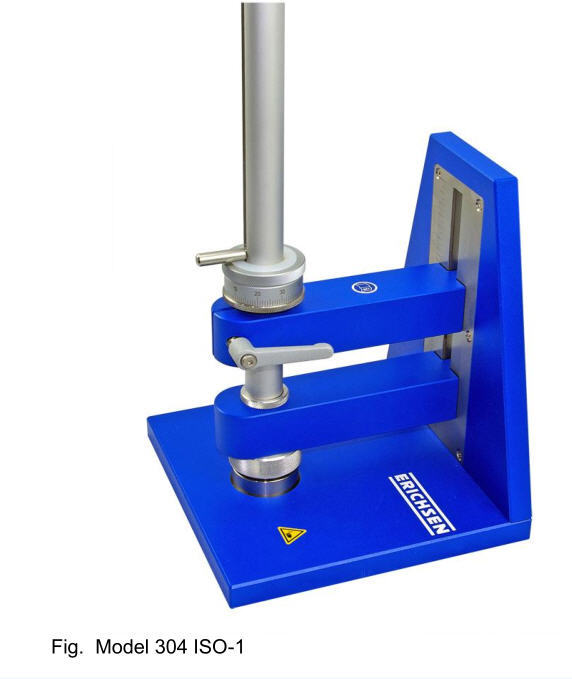
Principle of Variable Height Impact Test
Surface coatings are frequently subjected to impact and shock loads which deform the base material, thus placing stress on the adhesion and cohesion of the coating.
ERICHSEN Impact Tester 304 are used for determination of impact resistance, deformability and tensibility of coatings and substrates as well as adhesion of the coatings.
The ball impact test simulates this type of stress under standardised conditions.
A ball punch of defined weight the bottom of which is of fixed diameter, is dropped freely down a guide tube from an agreed or variable height.
In this case a defined weight, which sample-side end is formed as hemispherical head (ASTM and ISO-1) or as male die tappet with fixed diameter, is dropped freely down a guide tube from an agreed or variable height.
After the impact, the deformed zone of the specimen surface is examined for cracks and flaking.
The ball impact test is comparable to a dynamic version of the ERICHSEN Cupping Test.
Standards for Impact Tests
Mechanically the test instruments described in the various standards for impact tests are almost identical.
The important differences effect only the
- diameter of the punch end,
- inside diameter of the die,
- mass of the falling weight,
- scale for the dropping height/energy,
- clamping sleeves and stops to limit the indentation depth.
The following standard versions are available:
Impact Tester, Model 304 ASTM
(for test according to ASTM D 2794) consisting of:
- Basic plate and side plate with set-up and guide tube
- ASTM falling weight incl. ASTM hemispherical head (Ø 15,9 mm) – 1 kg
- ASTM die (inside Ø 16,3 mm)
Impact Tester, Model 304 ISO-1
(for test according to ISO 6272-1 – direct impact test) consisting of:
- Basic plate and side plate with set-up and guide tube
- ISO-1 falling weight incl. ISO hemispherical head (Ø 20 mm) – 1 kg
- Screw-on weight 1 kg (additional weight)
- ISO-1 die (Ø 27 mm)
- Additional arm with mounted specimen clamping device
- Impact depth limitation
Impact Tester, Model 304 ISO-2
(for test according to ISO 6272-2 – indirect impact test) consisting of:
- Basic plate and side plate with set-up and guide tube
- ISO-2 falling weight incl. male die tappet – 1 kg
- Male dies (Ø 12,7 mm and Ø 15,9 mm) incl. 1 tappet guide
- Screw-on weight (additional weight) 1 kg
- ISO-2 die (Ø 16,3 mm)
- Additional arm with mounted specimen clamping device
In the following table these instrument parameters are summarised and the standard versions of the ERICHSEN Impact Tester, Model 304, are shown in relation to the different impact test standards. | |||||
Standard | Ball Dia. | Die I.D | Falling Weight | Scale/Division | ERICHSEN Model |
ASTM D 2794 | 0.63“(15,9 mm) | 0.64“(16.3 mm) | 1 kg | 80/2 inch pounds | 304 ASTM |
ISO 6272-1 (direct impact) | 0.79" (20 mm) | 1,1“ (27 mm) | 1+1 kg ** | 1000/5 mm | 304 ISO-1 |
ISO 6272-2 (indirect impact) | 0,5“ (12,7 mm) & 0.63"(15,9 mm) | 0.64“(16.3 mm) | 1+1 kg ** | 1000/5 mm | 304 ISO-2 |
** The basic weight is doubled by bolting on a supplementary weight (up to 4 kg possible) |
Model 304 – General Description
The Impact Tester, Model 304, in all its variations, consists of a sturdy base plate with attached holding arm into which the slotted fall tube is clamped (transverse thread screw).
In the ISO versions the screw is tightened with a clamping lever enabling the apparatus to be set quickly for different specimen
thicknesses.
The lever can also be pulled out a short way against a spring force.
It is thus disengaged and can be turned freely.
Below the falling tube and carried in the base plate is mounted the die in accordance with the relevant standard.
The die is easily exchangeable but at the same time is accurately fitted so that the centre lines of guide tube and die coincide.
Located at the bottom end of the falling weight is the ball punch or male die tappet appropriate to the die being used on its side, it has a protruding pin which is guided in the slot along the length of the tube, used to lift the weight to the desired height manually.
On the ISO versions the mass of the falling weight can be doubled by bolting on an additional weight (a total weight up to 4 kg is possible).
Scales are mounted along the slot which in the case of instruments for ISO standards are considered in „cm“, or for ASTM instruments in „inch lbs“.
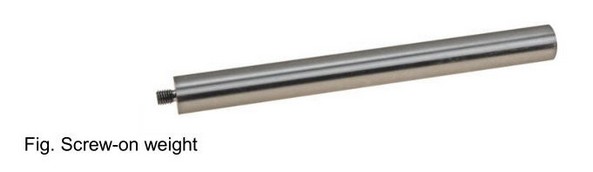
According to the standard the Model 304 ISO-1 for indirect impacts is equipped with a clamping sleeve to hold the test panel in position and with an adjustable impact depth limitation device. A movable ring over the falling tube is guided in the slot and clamped by means of a knurled screw and serves as stop for the pin protruding from the side of the falling weight.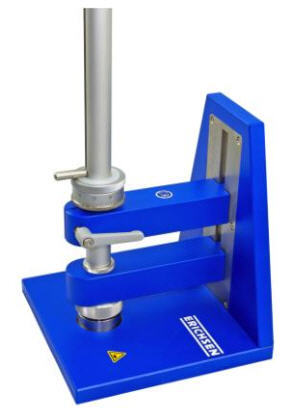
This arrangement provides for accurate pre-setting of the potential energy which is a considerable convenience when performing tests starting from a fixed height.
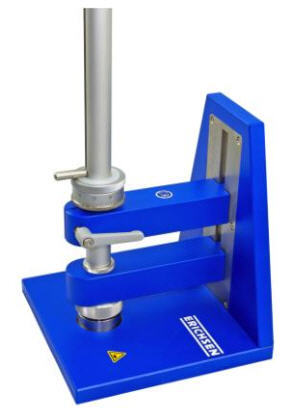
The indirect impact acc. to ISO-2 acts without the impact depth limitation.
The test relevant part of the accordingly used male die already rests onto the specimen to be tested.
During the test procedure, the falling weight attached with the tappet head impacts the upper plate of the used male die, by what the impact energy runs through the male die and finally affects at its lower end the specimen accordingly.
Procedure for the Impact Test
After preparing the specimen as laid down in the standards (in respect of surface treatment of base material, application of coating, hardening procedure, storage, coating thickness measurement, possible cross cut test etc.) two fundamental decisions have to be taken:
- The ball impact is directed onto the coating for a concave deformation (intrusion) or on the other side for a convex deformation (extrusion). The standards listed give the user the choice between these two, to select or make an agreement for one or the other method
- In respect of the energy for the deformation the first possibility is to employ an agreed value for the potential energy at the beginning of the fall. The impact test in this case gives the go/no-go test or pass/fail answer in respect of the resistance of the coating from the point of view of the formation of cracks under rapid deformation. This method gives only a qualitative result but enables a batch of specimens to be tested in rapid succession.
A quantitative result is obtained, if repeated impact tests are performed to establish the minimum energy to damage the material. In this case, the distance of drop and hence the energy of impact is varied until the formation of cracks and/or loss of adhesion is observed. The value of energy which resulted in such damage has to be confirmed by repeated tests using also further specimen panels. If different results are obtained, it is recommended to establish a mean value.
A fundamental point - and this applies also to the go/no-go test - is to ensure that the test is conducted at an adequate distance from the edge (at least 35 mm) and also from the previous tests on the specimen (minimum 70 mm centre to centre).
Evaluation and Interpretation
The specimens deformed by the ball impact are normally examined for cracks and peeling visually perhaps with the aid of a magnifying glass. To ensure that less obvious cracks will still be identified, the ASTM D 2794 standard suggests two more sensitive
methods of examination:
- Application to the specimen of copper sulphate solution to enable the smallest faults in the coating to be shown up in clear contrast. This procedure is only effective, if the base material is steel and if any anti-corrosion coating such as phosphating has also broken through as a result of the impact.
- In the case of electrically insulating coatings applied on a metallic base, the test area can also be examined with a porosity test instrument. For this, simple conductivity testers using a 9 VDC supply and a dampened sponge as test probe are all that is required. The impact energy is expressed in different terms in the individual standards. In ISO, DIN, NF and SNV the dropping height (in mm) in conjunction with the weight of the impact body is used for a relative energy scale. The remaining impact test standards lay down the use of absolute units of energy:
kg m (ISO 6272, ASTM D 2794), inch lbs (ASTM D 2794).
These units of energy relate to one another as follows: 0.1 kg m = 8.8 inch lbs
The conversion factors can be used to compare the energy values that can be set on the various versions of the instrument. Because of the differing ball and die dimensions, it is, however, not possible to convert results obtained with the different ball impact test methods by any method of accurate calculation.
Accessories

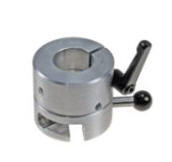
There is the option, to retrofit an existing standard Impact Tester 304 with retrofit kits that standardized tests according to ASTM, ISO-1 and ISO-2 can be performed.
Also available:

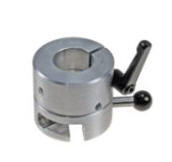
ISO Screw-on weight (1 kg) Hold-/Release Device for falling weight )
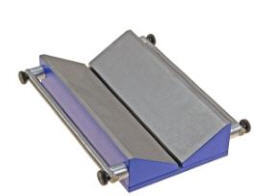
Safety Fixing Device "Prisma", wedge-shaped device for fixing round specimens (e.g. pipes), incl. 2 fixing belts
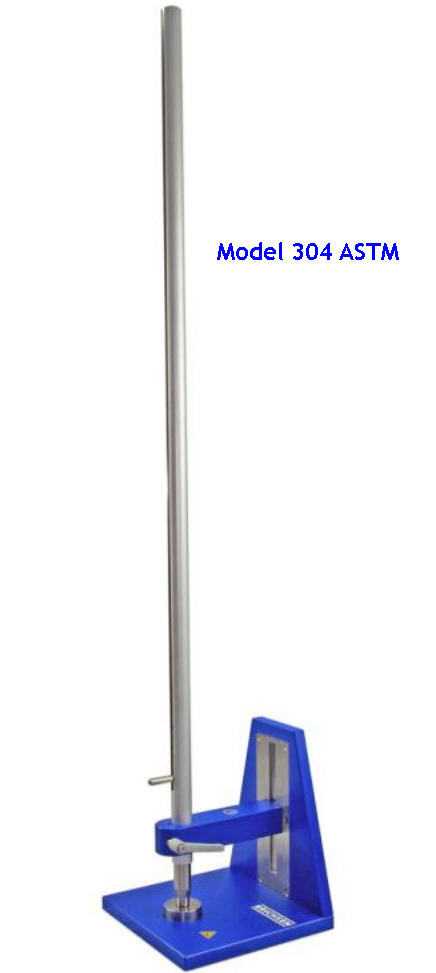
Samples to be used with impact
and conical mandrel tester.
ALU
Ref 284-ALU :
Alu 5754 (AIMg3) sample, 190 x 100 x 0,5 mm
STEEL
Ref 284-STEEL :
Cold rolled steel sample type DC04, 190x100x0,5 mm
GALVANISED STEEL
Ref 284-GALVASTEEL :
Zinc fire steel specimen type DX51D+Z275, 190x100x0,5mm
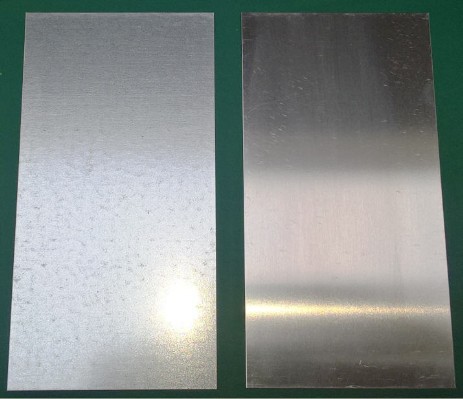